Overview
While tight exterior envelopes have become standard for single-family homes, similar construction practices have been slow to reach the multifamily sector. Multifamily buildings have many of the same leakage paths as houses, as well as additional paths hidden in walls or other cavities that are difficult to seal with conventional methods. Researchers recently developed an aerosol sealant to seal leaks in building walls, floors, and ceilings. The process has the potential to be more effective and convenient than conventional sealing methods because it requires less time and effort, and it can seal a larger portion of a leakage area more quickly.
The video below shows how the aerosol envelope sealing technology works.
This project measured envelope leakage reduction and final tightness, refined the unit preparation and sealing process, and modeled the impact of envelope tightness to estimate energy savings. The research team performed aerosol envelope air sealing on nine existing and 18 new construction multifamily units, and performed airflow and energy use modeling with EnergyPlus simulations for four ventilation strategies.
Results
The aerosol envelope sealing of new construction and existing building units successfully demonstrated high levels of air leakage reduction.
Air sealing — new construction
Reduction in new construction units varied from 67% to 94% with an average of 81%. All of the units were more than 50% tighter than the 3.0 ACH50 code requirement for low-rise residential buildings, and half of the units met the Passive House tightness requirement of 0.6 ACH50. ir sealing — existing buildings
Existing buildings achieved an average reduction in unit leakage of 68%. The pre-sealing results show initial leakage levels of 12.0 ACH50 to 17.0 ACH50 and post-sealing results from 1.4 ACH50 to 10.5 ACH50. With manual pre-sealing of larger leaks, the aerosol sealing process can reduce air leakage to meet or exceed the new construction low-rise residential code requirement of 3.0 ACH50.
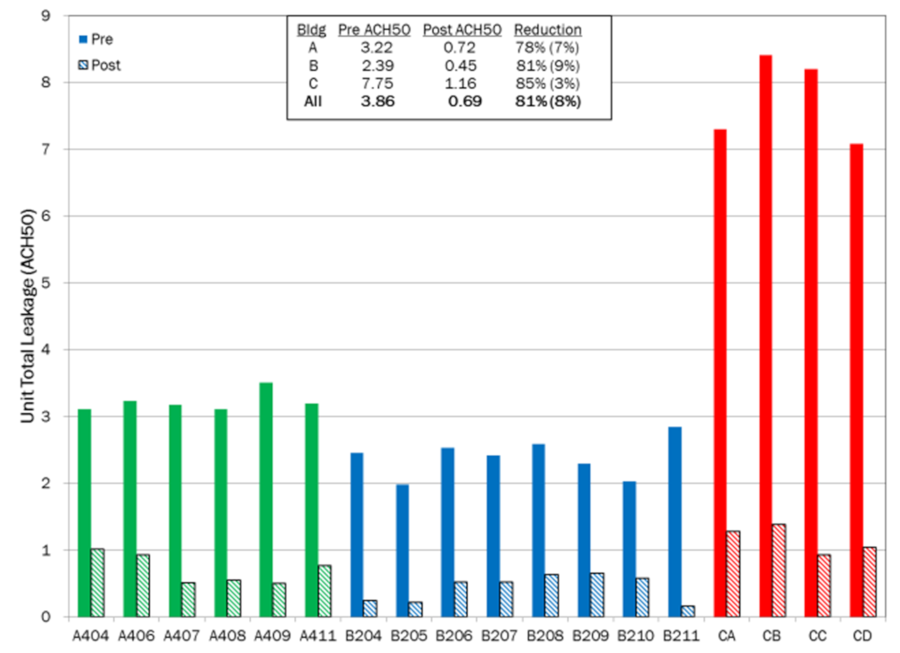
Air sealing — new construction
Air sealing — existing buildings
Existing buildings achieved an average reduction in unit leakage of 68%. The pre-sealing results show initial leakage levels of 12.0 ACH50 to 17.0 ACH50 and post-sealing results from 1.4 ACH50 to 10.5 ACH50. With manual pre-sealing of larger leaks, the aerosol sealing process can reduce air leakage to meet or exceed the new construction low-rise residential code requirement of 3.0 ACH50.
Energy savings modeling — new construction
The new construction modeling compared the energy performance for a building with a total (exterior and interior) envelope leakage of 3.0 ACH50 to a building sealed 80% tighter with the aerosol process. The 80% reduction in envelope leakage is approximately equal to the 81% average reduction for the aerosol sealing of the 18 new construction units completed for this project. The results show a 4% to 18% reduction in heating energy use with annual gas savings of 12 to 27 therms and cost savings from $7 to $16.
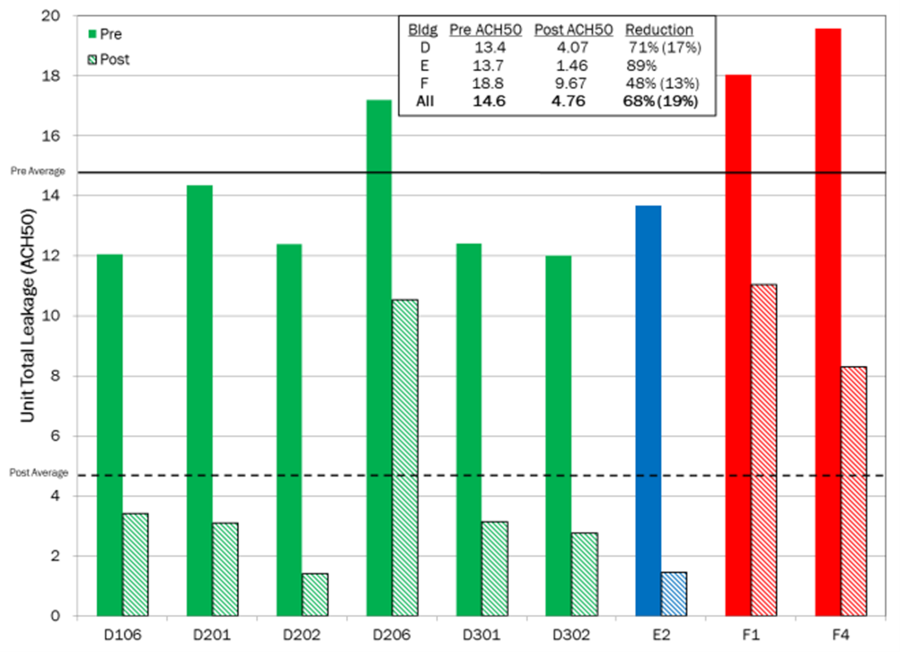
Air sealing results — existing buildings
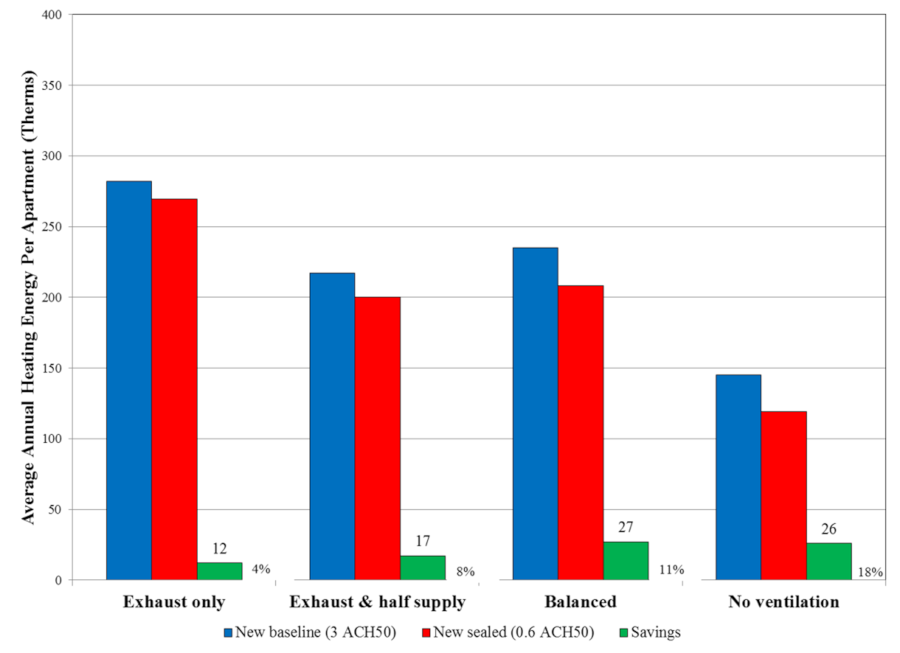
Energy savings modeling — new construction
Energy savings modeling — existing buildings
The modeling for existing construction focused on comparing the energy performance of an existing building sealed to the low-rise multifamily code requirement for new construction. The results show an 11% to 25% reduction in heating energy use with annual gas savings of 41 to 68 therms and cost savings from $24 to $39, which may not be sufficient for many building owners. However, the average starting leakage and resulting reduction of the nine existing units was much greater than the modeling assumption. Adjusting that assumption to match the reality of Minnesota’s existing building stock would increase annual savings by about a factor of two.
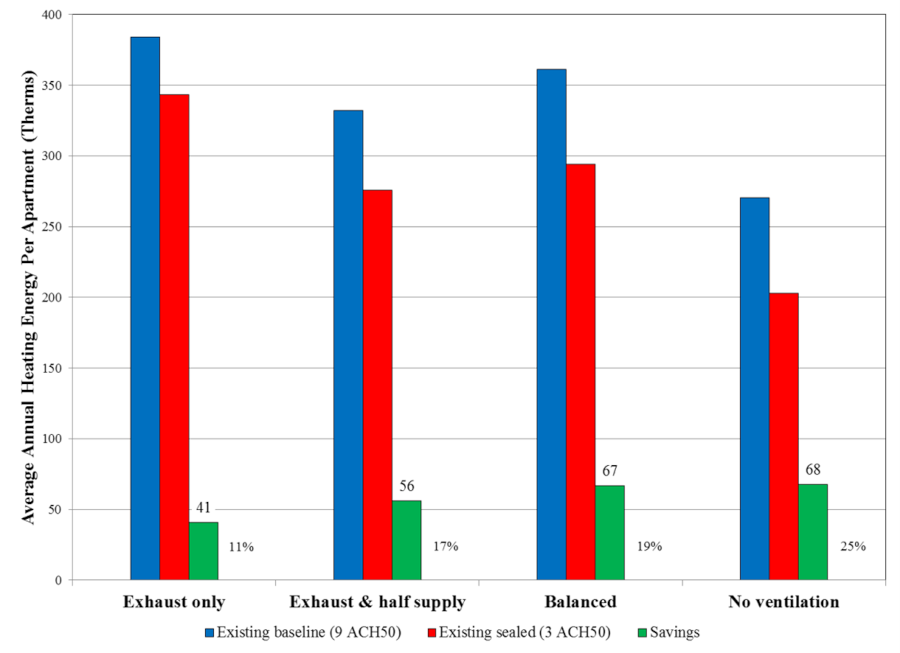
Energy savings modeling results — existing buildings
CIP Recommendations
Xcel Energy and CenterPoint Energy offer design assistance programs for new construction multifamily buildings, which can include a tighter building envelope and air infiltration reduction upon request. The modeled air infiltration results from this project should be used for baseline and reduced envelope tightness values.
All Minnesota utility programs for existing multifamily buildings should include incentives for envelope air sealing. Minnesota’s Technical Reference Manual needs to be updated to include methodology for computing multifamily envelope air sealing savings. The modeling results from this project can be used to provide an algorithm for calculating these savings.
Related Reports and Resources