Case Study: Riedell Skates Lighting Improvements
Project Background
Riedell Skates, a skating equipment manufacturer, was concerned about high electricity bills, lighting quality, and employee safety at their production facility in Red Wing, MN. Their old, inefficient bulbs and ballasts needed to be replaced constantly. They knew LED lighting could help them save money and reduce maintenance needs, but they didn’t know what type of lighting was best for their facility. When a One-Stop Efficiency Shop lighting consultant reached out, it was the nudge Riedell Skates needed to make the switch.
Facility Assessment
During a free lighting assessment, the lighting consultant determined the best LED replacement options for the space. He generated and presented a report that included recommended upgrades, rebates, energy savings, payback periods, and recommended qualified contractors for the project. Riedell Skates’ top priority was to create a safe and comfortable work environment. Their lighting consultant helped them find efficient lighting bright enough for employees to see well without being harsh on their eyes.
Improvements
With guidance from their lighting consultant, Riedell Skates installed Type B 4’ LED T8 lamps throughout the facility, eliminating the need for fluorescent ballasts while still using the existing fixtures. Their lighting consultant assisted them through the entire process including completing the rebate paperwork. Riedell Skates also took advantage of financing options from Center for Energy and Environment. After making the upgrades, the workspace is noticeably brighter and their electricity costs are down 19%.
We’ve been tracking our energy bill every month and since installing the new lights, our bill is down 19%.
Dan Johnson, Director of Manufacturing for Riedell Skates
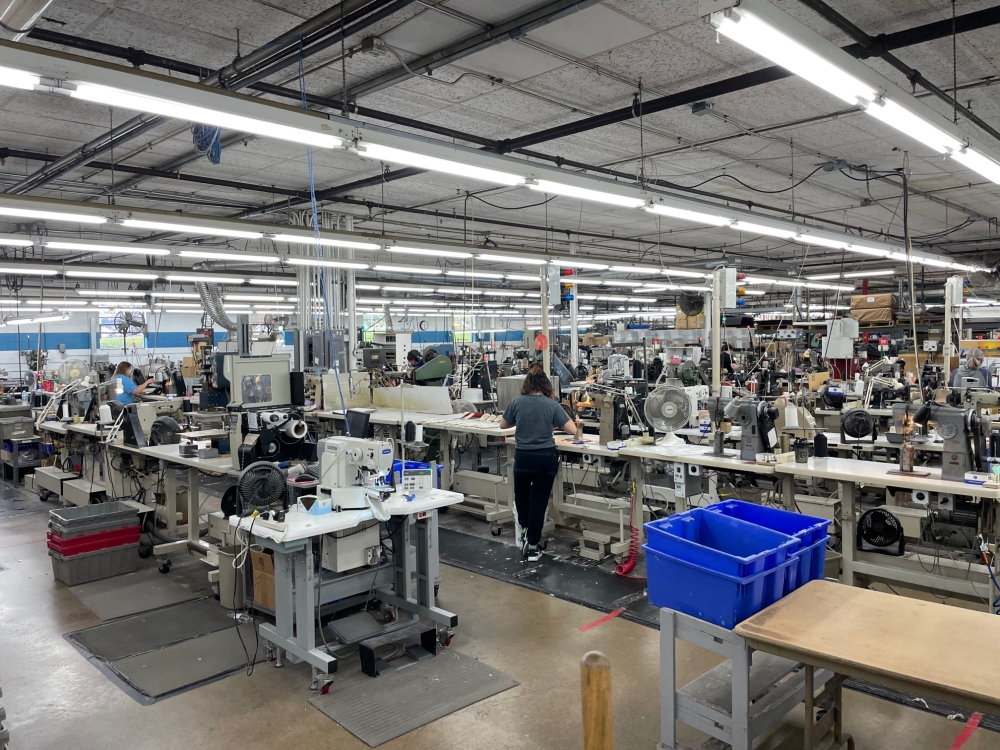
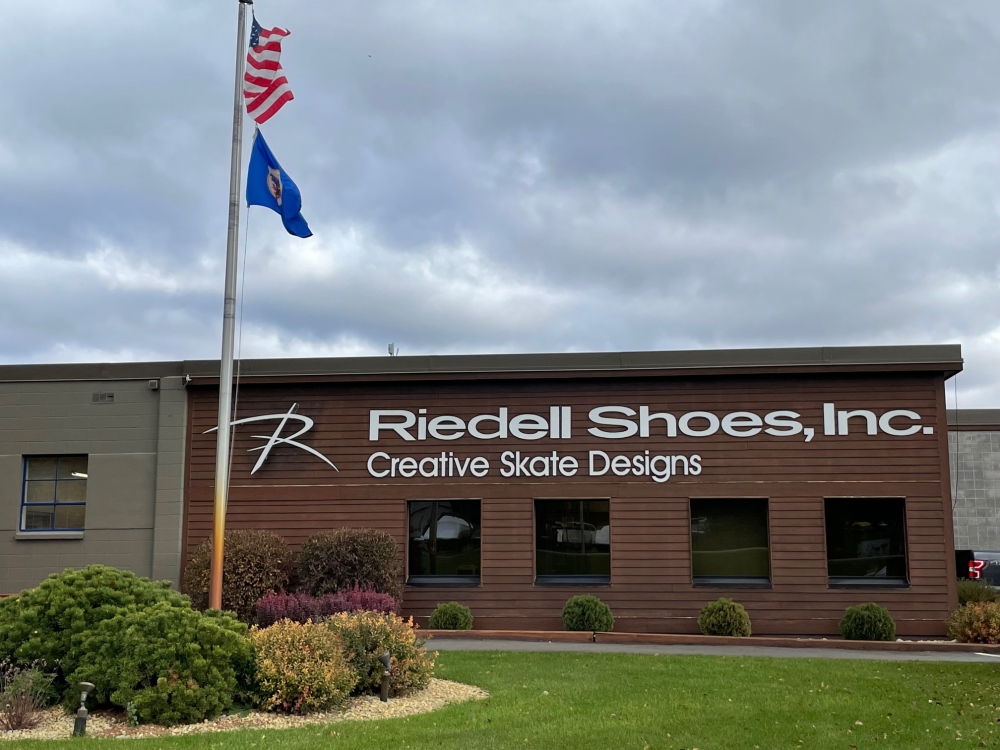
Project Impact
Problems
- Inefficient lighting and high electricity costs
- Frequent bulb and ballast changes
- Poor lighting quality in production area
- Employee safety concerns
Results
- Improved production floor lighting quality and brightness
- Increased employee safety
- Reduced maintenance needs
- Lowered electricity costs by 19%
Rebates and Savings
- $14,416 in annual savings
- 2.8 year payback period
- $16,391 rebate
- 128,253 kWh saved